POLYMERS
HOW CAN POLYMERS BENEFIT FROM E-BEAM TECHNOLOGY
Common chemical crosslinking agents such as peroxides and silanes pose safety concerns and require elevated temperatures to cure. These types of chemical processes can also yield noxious fumes and/or sensitizing by-products and require regulated disposal. Chemical crosslinking processes are affected by a large number of variables and imperfect process control can result in significant product loss.
Conversely, the crosslinking facilitated by e-beam processing does not require using additives nor does it generate hazardous chemical by-products. Crosslinking transforms a linear polymer into a three-dimensional molecule, resulting a significant increase in molecular mass, lower solubility in organic solvents and improved mechanical properties.
E-beam crosslinking is energy efficient. Since exposure time of the material to the beam is minimal (seconds), high throughputs are typical. E-beam technology is precisely controlled and the degree of crosslinking is directly related to the level of e-beam exposure. E-beam crosslinking is suitable for polymers which are difficult to crosslink chemically. Also, environmentally friendly alternatives such as e-beam crosslinked polyethylene can be created to replace less desirable plastics such as PVC.
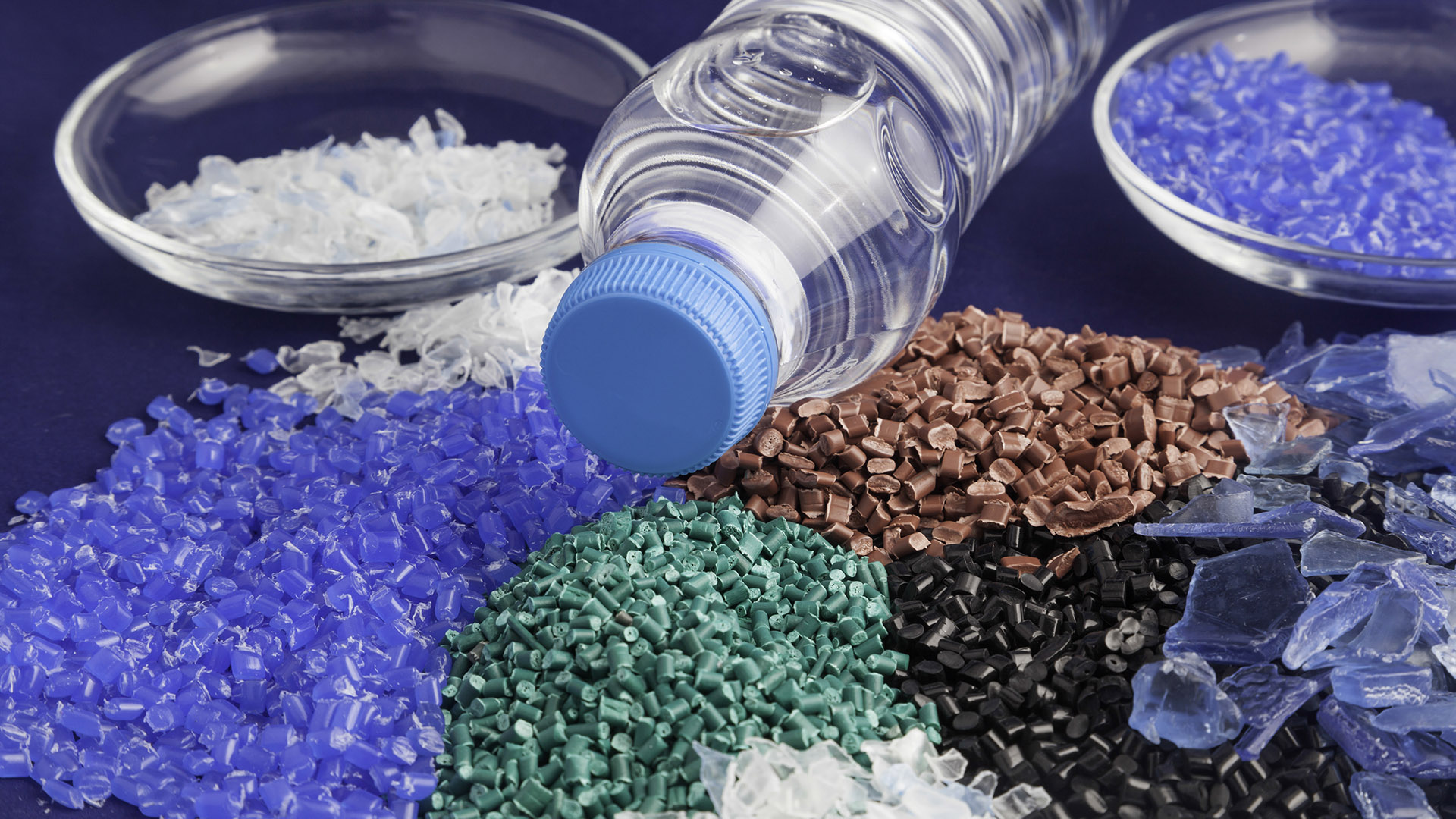
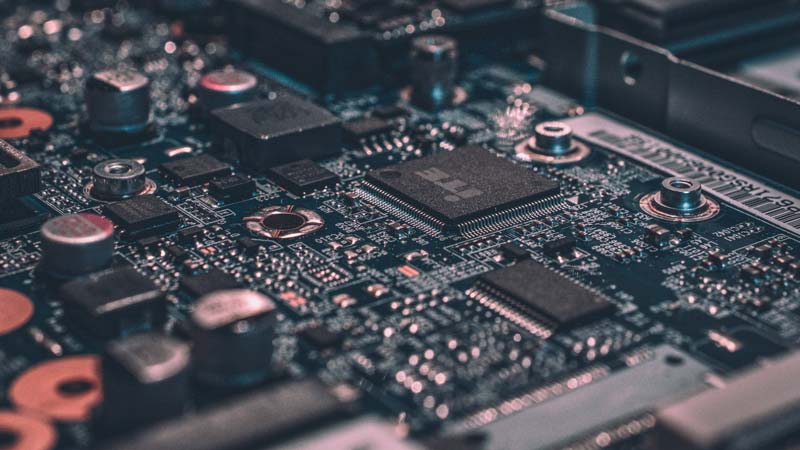
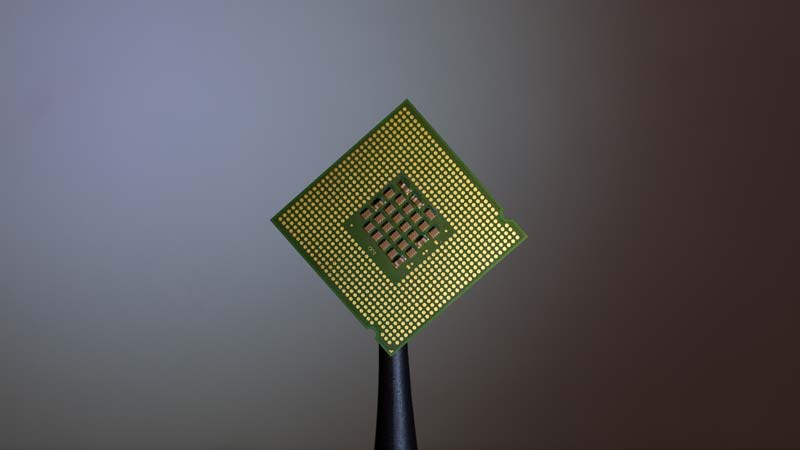
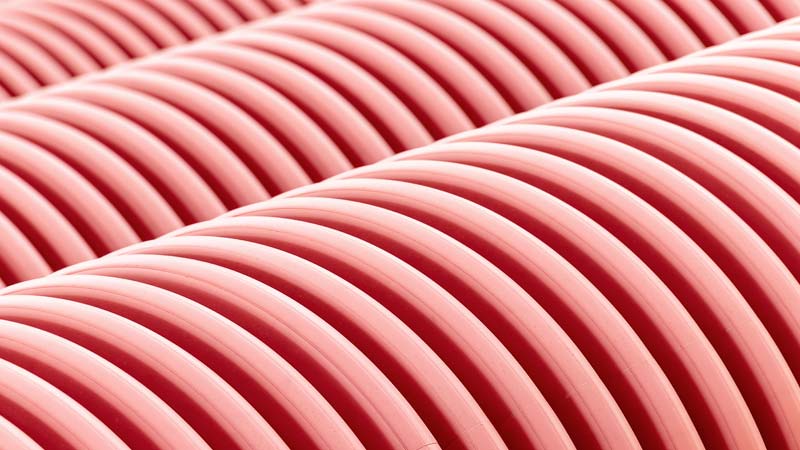
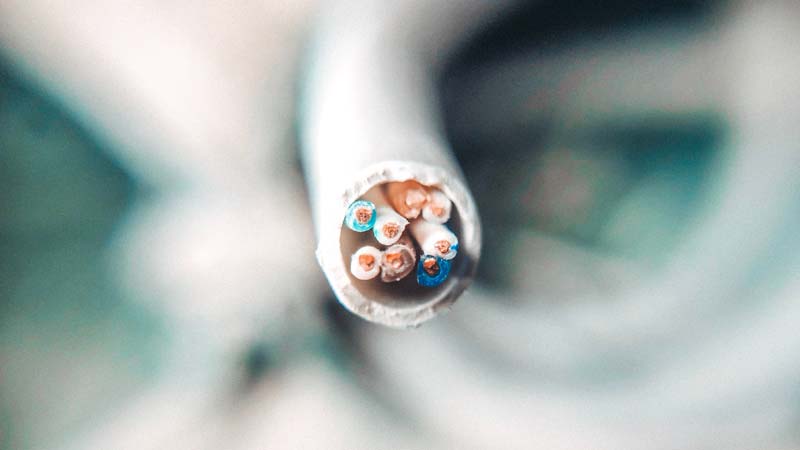
How E-beam works on crosslinking
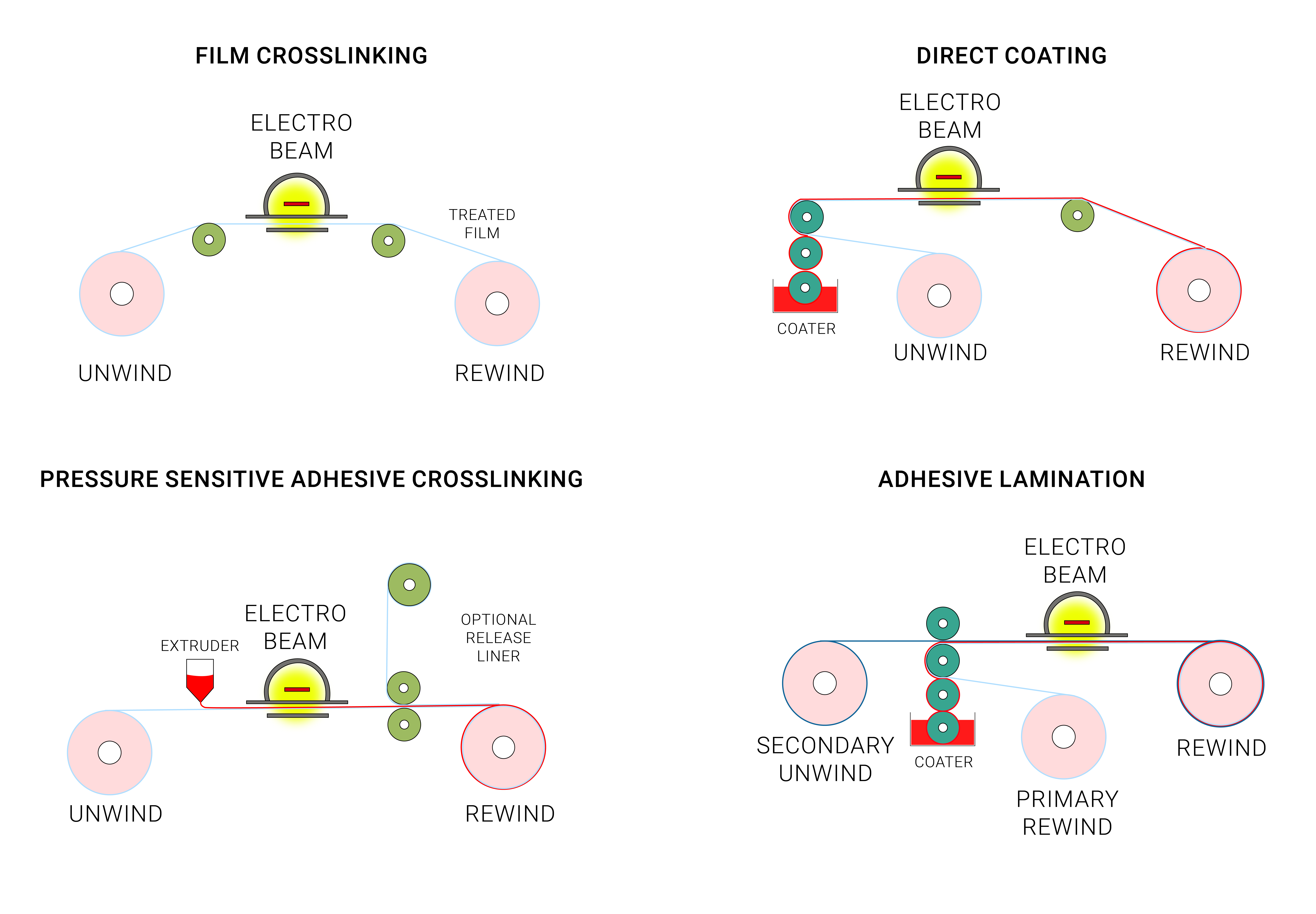
Use radiation-based modalities to achieve feature improvements
- Strength
- Elongation
- Memory
- Weight
- Water resistance
- Chemical resistance
- Temperature resistance
- Environmental stress crack resistance (ESCR)
Examples of commercial products that use e-beam crosslinking
- Wire and cable
- Jacketing
- Heat-shrinking products
- Gaskets, seals & other molded parts
- Piping and tubing
- Polyethylene foam sheet
- Hydrogels
Looking for a reliable scientific partner?
Contact Us
E: contact@pelegol.com